前言:不同工序可以产生不同形式的缺陷,但是,同一种形式的缺陷也可以来自不同的工序。由于产生锻件缺陷的原因往往与原材料生产过程和锻后热处理过程等多种因素有关,因此在分析锻件缺陷产生的原因时,不要孤立地来进行。
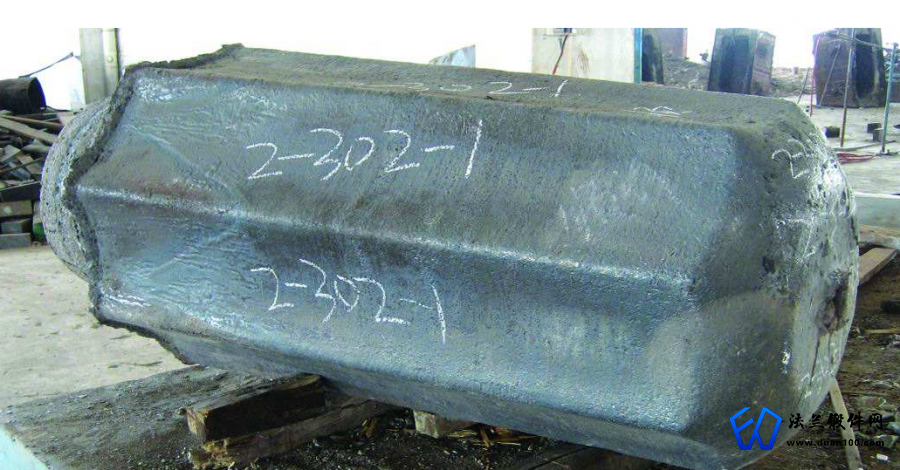
1、由原材料产生的缺焰
毛细裂纹(发裂):
位于钢材表面,深约0.5-1.5mm 的毛细裂纹,轧制钢材时,钢锭的皮下气泡被辗长而破裂形成的。锻前若不去掉,可能引锻件裂纹。
结疤:
在钢材表面局部地方存在的一层易剥落的薄膜,其厚度可达1.5imn左右。锻造时不能焊合,以结疤形态出现在锻件表面上。原因是浇注时,由于钢液飞溅而凝结在钢锭表面,轧制时被压成薄膜而贴附在轧材表面即为结疤。锻后经酸洗清理,结疤剥落,锻件表面上出现凹坑。
折缝(折叠):
在轧材端面上的直径两端出现方向相反的折缝。折缝同圆孤切线成一角度,折缝内有氧化夹杂,四周有脱碳。是由于轧辗上型槽定径不正确,或型槽磨损面产生的毛刺在轧制时被卷成折叠,锻前若 不去掉,将残留锻件表面。
非金属夹杂物:
在轧材的纵断面上出现被拉长了的,或被破碎但沿纵向断续分布的非金属夹杂。前者如硫化物,后者如氧化物、脆性硅酸盐。主要是由于在熔炼时,金属与炉气、容器之间发生化学反应形成的;另外,在熔炼浇注时由于耐火材料、砂子等落人钢液而引起。
展状断口:
往往出现在钢材的心部分。在钢材的断扣或断面上,出现一些与折断了的石板、树皮相似的形貌。这种缺陷在合金钢,特别是铬镍锏、铬镍钨钢中出现较多,在碳钢中也有发现。钢中存在非金属夹杂物,枝晶偏析、气孔、疏松等缺陷,在锻造过程中沿纵向被拉长.使钢材断口呈片层状。层状断口严重降低钢材横向力学性能, 锻造时极易沿分层破裂。
成分偏析带:
在某些合金结构钢.如40CrNiMoA、 38CrMoAlA等锻件的纵向低倍上,沿流线方向出现不同于流线的条状或条带状缺陷,缺陷区的显微硬度与正常区的明显不同。成分偏析带主要是由于原材料生产过程中合金元素发生偏析造成的轻微的成分偏析带对力学性影响不大,严重的偏析将明显降低锻件的塑性和韧性。
亮条或亮带:
在锻件表面或锻件加工过的表面上,出现长度不等的亮条。亮条大多沿锻件纵向分布。这种缺陷主要出现在钛合金和高温合金锻件中。由于合金元素偏析造成。钛合金锻件中的亮条,多属低铝低钒偏析区,高温合金锻件上的亮条区,多属铬钴等元素偏高亮条的存在使材料的塑性和韧性下降。
碳化物偏析级别不合格:
经常在高速钢、高铬冷变形模具钢等碳含量高的合金钢中出现,其特点是在局部区域有较多的破化物集聚,使碳化物偏析超过了许可的标准。由于钢中莱氏体共晶碳化物在开坯和轧制时未充分破碎,均匀分开所造成。严重的碳化物偏析容易引起锻件过热、过烧或开裂。
白点:
在钢坯的纵向断口上呈圆形或椭圆形的银白色斑点,在横向断口上呈细小的裂纹。白点的大小不一,长度为1-20mm或更长。白点在合金结构钢中常见,在普通碳钢中也有发现。由于钢中含氢较多和相变时组织应力大引起。大型钢坯锻轧后冷却较快时容易产生白点。白点是隐藏在内部的裂纹,降低钢的塑性和强度。白点是应力集中点,在交变裁荷作用下. 易引起疲劳裂纹。
缩孔残余:
在锻件低倍检査时,出现不规划的皱折状缝隙,形似裂纹,呈深褐色或灰白色;高倍检査缩孔残余附近有大量非金属夹杂物,质脆易剥落。由于钢锭冒口部分产生的集中缩孔未切除干净,开坯和轧制时残留在钢坯内部而产生的。
铝合金挤压棒村上的粗晶环:
经热处理后供应的铝合金挤压棒材. 在其横断面外层环形内出现粗大晶粒,称粗晶环。粗晶环的厚度.从棒材的开始挤出端至末端是逐渐增加的。主要是由于铝合金中含有Mn、Cr等元素以及挤压时金属与挤压筒壁之间的摩擦,使棒材表面层变形剧烈所致。具有粗晶环的坯料,锻造时容易开裂,如留在锻件上将降低零件性能。
铝合金氧化膜:
在锻件低倍侑上氧化膜沿金属流线分布,呈黑色短线状。在垂直于氧化膜纵向的断口上,氧化膜类似撕裂分层;在平行于氧化膜纵向的断口上,氧化膜呈片状或细小密集的点状。模锻件内的氧化膜,容易在腹板上或分型面附近见到。熔炼时铝液中没有去除的氧化物夹杂,在浇注过程中由表面卷入金属液内,在挤压、锻造等变形过程中被拉长、变薄而成为氧化膜 。氧化膜对锻件纵向力学性能影响小,对橫向,特明是短横向力学性能的影响较大。按照锻件类别和氧化膜标准进行比较,不合格的才报废。

2、由下料产生的缺陷
切斜:
坯料端面与坯料袖线倾斜,超过了许可的规定值。剪切时棒料未压紧造成的。切斜的坯料镦粗时容易弯曲、模锻时不好定位,易形成折叠。
坯料端部弯曲并带毛刺:
切料时部分金属被带人剪刀间隙之间,形成尖锐的毛刺,坯料端部有弯曲变形。由于剪刀片之间间隙太大,或刃口不锐利造成有毛刺的坯料,锻造时容易产生折叠。
坯料端部凹陷或凸起:
坯料端面中心部分金属是拉断的,因而端面上出现凸起或凹陷。原因是刀片之间的间隙太小,坯料中心部分金属不是被剪断的而是拉断的,使部分金属被拉掉。这样的坯料锻造时容易产生折叠和裂纹。
端部裂纹:
主要是在剪切大截面坯料时出现,在冷态下剪切合金钢或高碳钢时,也有这种裂纹。由于材料硬度过高、剪切时刀片上的单位压力太大而引起。锻造将使端部裂纹进一步扩大。
凸芯开裂:
车床下料时,在坯料端面上往往留有凸芯,若未去掉.则在锻造时可能导致在凸芯周围形成开裂。由于凸芯截面小、冷却快;端面面积大、冷却慢、因而导致在凸芯周围形成裂纹。
气割裂纹:
一般位于坯料端面或端部,裂口是粗糙的。气割前没有充分预热,导致形成较大热应力而引起。
砂轮切割裂纹:
高温合金在冷态下用砂轮切割时,往往导致在端面产生裂纹。这种裂纹有时要在加热之后才能用肉眼看到。高温合金导热性差,砂轮切割产生的大量热量不能迅速传导出去,在切割断面上形成很大热应力,甚至产生微小裂纹。加热时再次产生较大热应力,使微小裂纹扩大成肉眼可见裂纹。
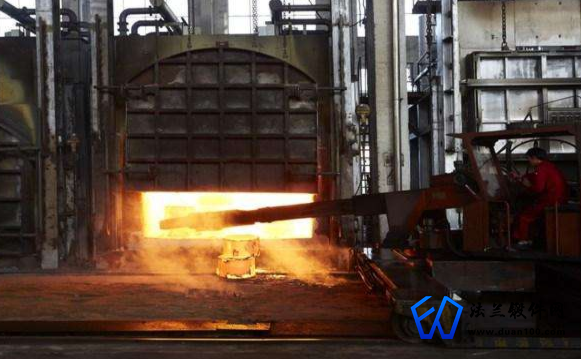
3、由于加热产生的缺陷
过热:
由于加热温度过高造成晶粒粗大的现 象。碳钢过热的特征是出现魏氏组织;工模具钢以一次碳化物为特征,某些合金结构钢如!8Cr2Ni4WA, 20Cr2Ni4A.过热后除晶粒粗大外,还有MuS沿界析出,对后者用通常的热处理方法不易消除。原因是加热温度过高或时间过长、或由于没有考虑到变形热效应的影响而引起过热将使钢锻件的力学性能,特别是塑性和冲击轫度降低。在一般情况下,通过退火或正火可使钢锻件的过热消除。
“蛤蟆皮”表面:
铝合金、筒合金的坯料,在镦粗时表面形成“蛤蟆皮”或者出现类似皮的粗糙表面,严重时还要开裂。由于坯料过热,晶粒粗大而引起。有粗晶环的铝合金毛坏,仵镦粗时也会出现这种现象。
魏氏α相或β脆性:
(α+β)钛合金坏料过热后,其显微组织的特征是,a相沿粗大的原始β晶粒晶界和晶内呈粗条状析出。晶内析出的粗条状α相.各按一定的方向排列,即形成所谓的魏氏a相。由于加热温度超过了 (α+β)钛合金的β转变温度而引起有魏氏α相的钛合金锻件,其拉伸塑性指标明显降低,这就是所谓的β跪性热处理不能消除β膽性。
钢锻件的过烧:
过烧部位的晶粒特别粗大,氧化特別严重,裂口间的表面呈浅灰蓝色。碳钢和合金结构刚过烧后,晶界出现氧化和熔化。工模具刚过烧后,晶界因熔化而出现鱼骨状莱氏体。由于炉温过度或坯料在高温区停留时间过长而引起。炉中的氧沿晶界渗透到晶粒之间,发生氧化或形成易熔的氧化物共晶使晶粒间联系遭到破坏。
铝锻件的过烧:
表面呈黑色或暗黑色,有时表面还有鸡皮状气泡,铝合金坯料过烧后,其显微组织中将出现晶界熔化、三角晶界或复熔球。只要有其中的一种现象存在即 为过烧。铝合金坯料加热温度过高时,强化相熔化,冷却下来后,在显微组织中即可看到晶界加粗、三角晶界或复熔球之类的特殊形态。
加热裂纹:
一般是沿坏料的横断面开裂,而且裂纹是由中心向四周扩展的。这种裂纹多产生于高温合金和高合金钢钢锭和钢坏加热。由于坯料尺寸大,导热性差而加热速度又过快,在坯料中心和表层之间温差大,由此产生的热应力超过了坯料的强度所致。
铜脆:
钢锻件表面上出现龟裂。高倍检查,有铜沿晶界分布 。在加热过铜料的炉子中加热钠料时易产生这种缺陷。炉内残存的氧化铜屑,加热时被铁还原为自由銅。熔融的铜原子在高温下沿奥氏体晶界扩 散,削弱了晶粒间的联系所致。
蔡状断口:
在钢锻件的断口上出现一些像蔡晶体一样的闪闪发亮的小平面。这种缺餡在合金结构钢和高速钢中容易见到。由于加热温度过高或终锻温度高,变形量又不够大而引起。萘状断口的实质是过热。因而将降低钢锻件的塑性和韧性。
石状断口:
是合金结构钢严重过热后出现的一种缺陷。石状断口是在调质状态下现察到的,具特征是在纤锥状断口基体上出现,—些尤金属光泽的、像水泥一样的灰白色小平面。用热处理方法不能消除它,因而是一种不许可的缺焰。加热温度过高,使MnS大量溶解,熔于钢中的MnS在冷却时,以极细致点沉淀在粗大的奥氏休晶界上,削弱了晶界的结合力,调质处理使钢基体的韧性加强以后,钢在折断时便沿奥氏体晶界断裂,从时在断口上形成一些无光泽的灰白色的过热小水平面。具有石状断口的锻件应报废。
低倍粗晶:
低倍粗晶是合金结构钢锻件过热后的另一种反映、其特征是,在锻件的酸侵低倍试片上,呈现肉眼可见的多边形晶粒,严重时这些多边形晶粒看起来呈雪片状。过热的奥氏体晶粒晶界比较稳定,通常的热处理可以将其消除。而再结晶仅在粗大的奥氏体晶内进行,在一个典氏体晶粒内生成了若干个新的小晶粒。由于小晶粒晶界较薄或位向差别不大,因而在低倍上看到的仍是原始的奥氏休粗大晶粒即低倍粗晶。
脱碳:
钢件表层的含磷量比内部的明显降低,硬度值比要求的低。在高倍组织上表层的渗碳体数量减少。在氧化性气氛中加热高碳钢,含硅量多的钢时最易脱碳。钢在高温下表层的碳被氧化。脱碳层深度由0.01-0.6mm,视钢的成分、炉气成分、温度和加热时间的长短而定脱碳使零件的强度和疲劳性能下降、磨损抗力减弱。
增碳:
经油炉加热的锻件,其表面或部分表面碳含量明显提高,硬度增大,增碳层的碳的质量分数可达1%左右,局部点甚至超过2%,出现莱氏体组织,増碳厚度有的达到1.5-1.6mm。坯料的油炉里加热时,两个噴嘴的喷射交叉区得不到充分燃烧,或喷嘴雾化不良喷出油滴,使锻件表面产生增碳。增碳的锻件,切削时易打刀。
未热透引起的心部开裂:
常在坏料头部出现心部开裂,其开裂深度与加热和锻造有关,有时裂纹沿纵向贯穿整个坯料。由于保温时间不够未热透,心部塑性低而引起。高温合金导热性差,若坯料截面尺寸大,应注意给予足够的保温时间。
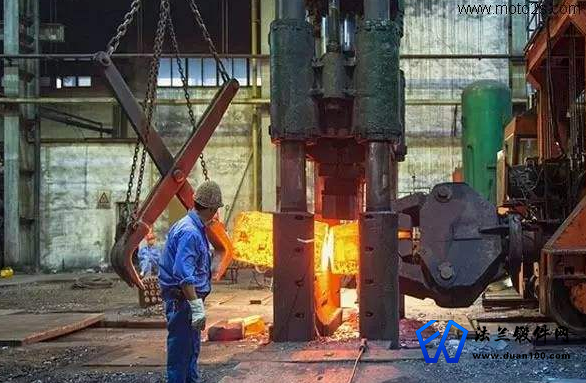
4、由锻造产生的缺陷
鼓肚表面纵裂:
自由嫩粗时,在毛坯的鼓肚表由上由于拉应力作用,产生不规則的纵向裂纹。由于毛坯与砧块接触面间存在摩擦力,引起不均匀变形而出现鼓肚,若一次燉粗量过大,就会产生纵裂。
十宇裂纹 (纵向内裂):
这种裂纹常在低塑性的高速钢、高铬钢的拔长工序中产生。十宇裂纹沿锻件横断面对角线分布,其枞向扩展深度不—,严重的可以赏穿整个毛坯长度。在反复翩转90°的拔长过程中。若送时量过大,则在毛坯横截面的对角线上将产生最大的交变剪切,当切应力超过材料许可值时,便沿对角线方向产生裂纹。
纵向条状裂纹:
主要出现在对料进行抜长由圆形压成方形时,或在拔长后将坯料倒拔、滾圆时。在横截面上,裂纹出现在中间部分呈条状,裂纹沿纵向的扩展深度不一,与锻造搡作有关。在用平砧对毛坯进行倒按或滾圆时,毛坯的水平方向有拉应力出现,此拉应力沿毛坏表面向中心增大在中心处达最大值,当其超过材料強度后便形成纵向内裂。
角裂:
在拔长后坯料的四根被上零散出现的拉裂裂口。角裂多出现在高速钢、高铬钢坯料的拔长工序中。 坏料拔长成方后,棱角部分温度下降,棱角与本体部分的力学性能差异增大。棱角部分因金属流动闲难产生拉应力而开裂。
内部横向裂纹:
在坯料枞向断面上沿高度方向出现的条状裂纹。高速钢、高铬钢坯料拔长时,若送进比小于0.5,则易产生这种裂纹。当拔长时的送料比小于0.5时、在坏料轴向将产生拉应力。当其超过坯料中某薄弱 处的材料抗拉强度时,便要在该处引起横向裂纹。
冲孔裂纹:
在冲孔边缘沿径向出现的裂纹。在铬钢冲孔时出现较多。由于冲孔芯子没有预热、预热不足或一次冲孔变形量太大而引起。
双相锻造裂纹:
模锻奥氏体、铁素体或半马氏体不锈钢坯料时,沿α相和γ相的界面或强度较低的α相出现的开裂。由于过剩α相太多(在奥氏体、铁素体不锈钢中α相超过12%、在半马氏体钢中α相超过10%)和加热温度偏高所引起。
分型面裂纹:
模锻件沿分塑面出现开裂,常常要切边后才显露出来。原材料非金属夹杂物多,有缩孔残余或疏松,模锻时挤入分型面所致
穿筋:
在具有L形、U形和H形截面的模锻件筋条或凸台的根部,出现的与分型面平行的裂缝。由于坏料过多,筋条充满后,腹板上多余金属较多,在继续模锻时,腹板上多余金属向飞边榷剧烈流动,在筋条根部产生较大剪应力。当其超过金属抗抑强度后,便形成穿筋。
剪切带:
锻件横向低倍上出现流浪状的细晶区。多出现在钛合金和低温锻造的高温合金锻件中。由于钛合金和高温合金对激冷敏感性大,模锻过程中,接触面附近难变形汉逐步扩大,在难变形区边界发生强烈剪切变形所致。结果形成了强烈方向性,使锻件性能下降。
带状组织:
铁素体或其他基体相在锻件中呈带状分布的一种组织。多出现在亚共析钢、奥氏体一铁素体不锈钢和半马氏体钢中。由于在两相共存情况下锻造变形产生的它降低材料的横向塑性指标,容易沿铁素体带或两相的变界处开裂。
锻件流线分布不当:
在锻件低倍上出现流线断开、回流、涡流对流等流线亲乱现象。由于模具设计不当,坯料尺寸、形状不合理以及锻造方法选择得不好所引起。
折叠:
在外规上折叠与裂纹相似,在低倍试片上折叠外流线发生弯曲、如果是裂纹、则流线被切断。在高倍试片上,与裂纹底部尖细不间,折叠底端圆钝,两侧氧化较严重。折叠是锻造过程中已氧化过的表层金属汇合在一起而形成的。自由锻件上的折叠,主要是由干拔长时送时量太小,压下量太大或砧块圆角半径太小而引起;模锻件上的折叠,则主要是模锻时金属发生对流成或回流造成的。
晶粒不均匀:
锻件中某些部位的晶粒特别粗大,另外一些部位却较小,形成晶粒不均匀耐热钢及高温合金对晶粒不均匀特别敏感。始锻温度过高,变形量不足,使局部区域的变形程度落入临界变形;或者终锻温 度偏低,使高温合金坯料局部有加工硬化,淬火加热时该部分晶粒严重长大。晶粒不均匀会引起持久性能,疲劳性能下降。
铸造组织残留:
如果残留有铸造组织,锻件的伸长率和疲劳强度往往不合格。在低倍试件上,残留铸造组织部分的流线不明显. 甚至可以见到树枝状晶。主要出现在用铸锭作坯料的锻件中。由于锻比不够大或锻造方法不当引, 这种缺陷使锻件的性能下降,尤其是冲击韧度和疲劳性能下降更多。
局部充填不足:
锻件凸起部分的顶端或棱角充填不足的现象、主要发生在模锻件的筋条、凸肩转角等处,使锻件轮廓不清晰。毛坯加热不足、金属流动性不好、预锻摸瞠和制坯摸瞠设计不合理、设备吨位偏小等都可能引起出现这种缺陷。
模锻不足:
锻件在与分型面垂直方向上的所有尺寸都增大,即超过了图样上规定的尺寸。这种缺陷最容易出现在锤上模锻件上。飞边桥部阻力过大,设备吨位不足,毛坯体积或尺寸偏大,锻造温度偏低,模膛 磨损过大等均可引起欠压。
错差:
模锻件上半部相对下半部沿分甩面产生了铕位。锻模安装不正或锤头与导轨之间间隙过大;或者锻模上没有平衡镨位的锁口或导柱。
表面鱼鳞状伤痕:
模锻件局部表面很粗糙,出现鱼鳞状伤痕。在模锻奥氏体和马氏体不锈钢时,最容易产生这种表面缺陷。由于润滑剂选择不当,润滑剂质量欠佳,或者由于润滑剂涂抹不均匀,造成了局部粘模所致。
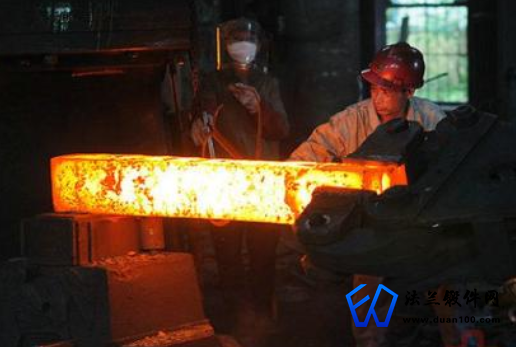
5、由于切边产生的缺陷
切边裂纹:
切边时,在分裂面处产生的裂纹。由于材料塑性低,在切边时引起开裂。镁合金模锻件切边温度过低;铜合金模锻件切边温度过高都会产生这种裂纹。
残留毛刺:
切边后沿模锻件分型面四周围留下大于0.5mm的毛刺,如果切边后尚需校正,则残留毛刺将被压入锻件体内而形成折叠。切边模间隙过大,刃口磨损过度,或者切边模的安装与调整不精确,均可以引起残留毛刺。
表面压伤:
模锻件与凸模的局部接接触面上,出现压痕或压伤。由于凸膜与模与模缎件接触面部分的形状不吻合.或推压面太小造成。
弯曲或扭曲变形:
横锻件在切边时出现的弯曲或扭曲变形。在细长、扁簿、形状复杂的模锻件上容易发生。由于切边凸模锻件的接触面太小,或出现了不均匀接融而引起。
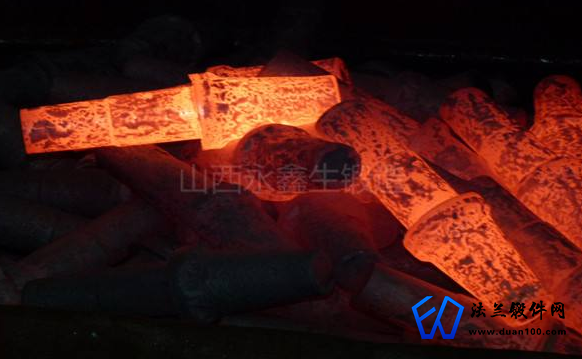
6、锻后冷却不当产生的缺陷
冷却裂纹:
裂纹光滑钿长,有时呈网状龟裂。高倍现察:裂纹附近出现马氏体组织,无塑性变形痕迹。多在马氏体钢锻件上发生。由于锻后冷却过快,产生了较大的热应力和组织应力所致。在200℃左右砂坑或炉渣中缓冷可以防止此种裂纹。
冷却变形:
大型、薄壁、细筋框架式构件,在锻后冷却过程中发生的翘曲变形。由于锻造中产生的残余应力和冷却不均匀引起的应力相互作用而引起。锻后立即退火可以防止此种缺陷。
475℃脆性裂纹:
铁素体不锈钢锻后冷却过慢,在通过400-520℃温度区间的停留时间过长而出现的表面裂纹。由亍在400-520℃停留时间过长,促使某种特殊物质析出而导致脆性。在400-520℃快冷可以防止裂纹。
网状碳化物:
碳化物沿晶界呈网状析出,使锻件塑性和韧性下降。这种缺陷在碳含虽高的钢锻件中经常可以见到 由于设后冷却缓慢,使碳化物得以沿晶界折出,它使锻件在淬火时容易裂纹,恶化零件的使用性能。
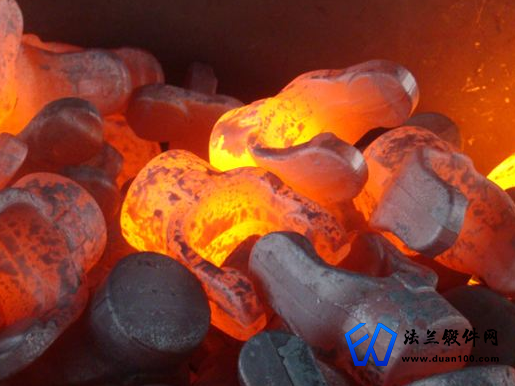
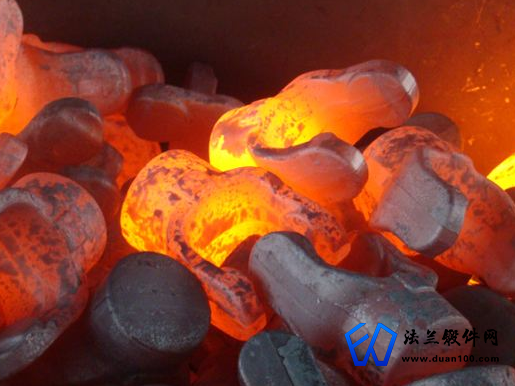
7、锻后热处理产生的缺陷
硬度过高:
锻件在热处理后检查硬度时、测得的硬度比技术条件要求的高。由子正火后冷却过快,或钢的化学成分不合格等所引起。
硬度偏低:
锻件硬度比技术条件要求的低。由于淬火温度偏低、回火温度偏高、或者多次加热引起表层严重脱碳而造成。
硬度不均(有软点):
在同一锻件上不同部位的硬度相差很大,局部地方的硬度偏低。由干一次装炉量太多,保温时间太短或局部有严重脱碳而引起。
变形:
在热处理过程,特别是在淬火中,锻件发生变形。由于热处理工艺不合理、冷却方式不当引起。
淬裂:
在锻件的尖角等应力集中处开裂。与锻造裂纹不同,淬火裂纹的内侧壁表面上没有氧化与脱碳现象。由于没有进行预备热处理、淬火温度太高、冷却速度过快以及锻件内部有夹杂物等缺陷所引起。
黑色断口:
断口呈暗灰色或近似黑色。在显微组织中,有棉絮状的石墨分布在不均匀的球状珠光体上。多在高碳工具钢锻件出现。由于锻后退火时间过长,或经过多次退火处理,从而促进了钢的石墨化过程和石墨碳的析出所造成的。
8、锻件在清理过程中产生的缺陷
过腐蚀:
在锻件表面上出现麻坑或麻点,呈琉松多孔状。由于酸洗溶液变质,酸洗时间过长,或者有酸液残留在锻件上所致。
腐蚀裂纹:
多出现在马氏体不锈钢锻件上,其特征是在锻件表面上有细小网状裂纹,在显微组织中裂纹沿晶界扩展。由于锻后锻件上的残余应力未及时消除,在酸洗过程中产生了应力腐蚀而导致形成裂纹。
局部过热裂纹:
在表面用砂轮清理时出现的裂纹。在铁素体不锈钢锻件上容易发生。用砂轮打磨引起局部过热所致。可改用风铲来清理其表面缺陷。
更多法兰锻件资讯,就上法兰锻件网